Additive Manufacturing of a Wireless Ceramic High Temperature and Pressure Sensor
Maintaining situational awareness of the weapon environment is desirable for developing the next generation of robust missile and munition (M&M) systems that can withstand the extreme acceleration, temperature, and pressure conditions that are presented by traditional fighter and hypersonic aircraft. In addition, tracking the temperature and pressure of high temperature turbines used in turbojets both for aircraft and energy production is highly desirable. Conventional techniques for remotely monitoring munition assets are primarily performed by proximate environmental monitoring by fuel sensors, accelerometers, surface acoustic wave sensors, chemical resistors, and temperature sensors. These are limited to storage and transportation purposes and typically have a limited temperature range, e.g., -55 °C to 125 °C.
Conventional temperature sensors used in the evaluation of M&M systems and turbine systems include thermocouples, thermistors, resistance thermometers, quartz thermometers, which all include a metallic coil inductor. Due to the oxidation of the metallic coil inductor, these temperature sensors cannot be used in high temperature environments for prolonged periods of time and can only be used under wired measurement conditions.
Conventional pressure sensors used in these applications include passive pressure sensors based on resistive or capacitive sensing mechanisms. These sensors also require a wire interconnection and they cannot operate effectively in high temperature environments. Moreover, pressure sensors that utilize a patch antenna operate within a limited temperature range, e.g., -55 °C to 125 °C, because of the metallic wire used with the patch antenna.
The technology developed at FSU comprises a wireless temperature and pressure sensor which includes a ceramic coil inductor having ceramic material and a relatively high volume fraction of carbon nanotubes. The combination leverages the remarkable electrical and mechanical properties (stiff and strong) of carbon nanotubes (CNTs) and the thermal properties (temperature sensitivity) of ceramic materials.
Generally, the temperature sensors comprise a ceramic coil inductor that is formed of a ceramic composite and a thin film polymer-derived ceramic (PDC) nanocomposite having a dielectric constant that increases monotonically with temperature and the pressure sensors comprise a ceramic coil inductor formed of a ceramic composite, which includes carbon nanotubes and/or carbon nanofibers. This novel technology has the potential to revolutionize the space industry, defense industry, and engineering.
Advantages
-
The ability to provide real-time, in-flight monitoring of systems that operate in high temperature and pressure environments
-
The ability to maintain safety and effectiveness of critical parts and materials without the need for extensive nondestructive evaluation (NDE) (for temperature sensors), thereby reducing cost and time
-
On-demand tracking and assessing of the status of systems over extended periods, based upon changing conditions
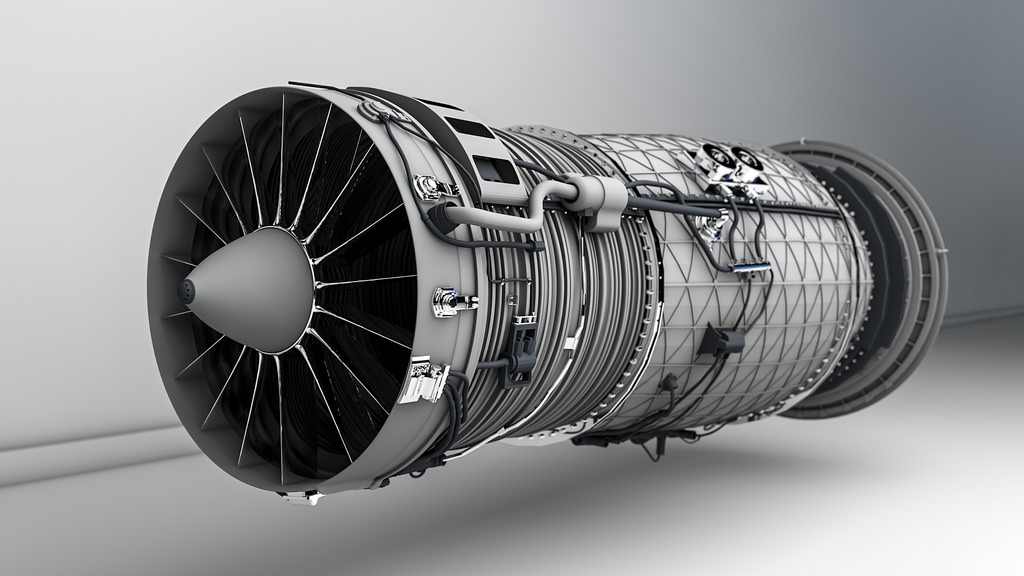
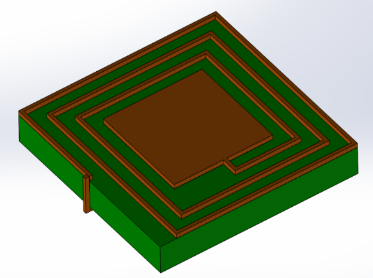
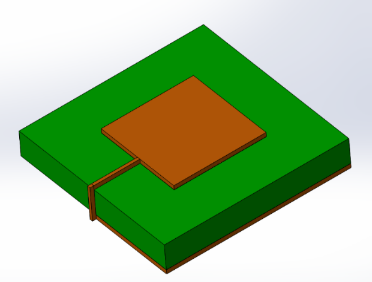
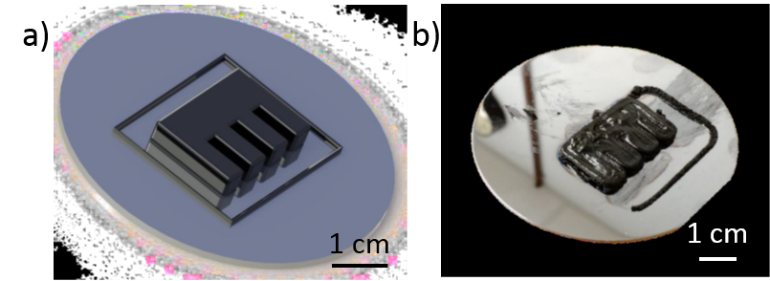