Solderless Joint Technology
This is a simple, yet novel device that eliminates the need for any type of solder when joining two large cables. The Solderless Joint Technology will immediately save hundreds of thousands of dollars in manufacturing costs, as well as minimize the risk to the entire multi-million dollar superconducting magnet system. This device has been fabricated and tested by the team in the laboratory and has yielded amazing results.
This invention eliminates the need for solder by placing wires in a compression box that seals them between a novel cradle of steel and copper. These cradles are compressed by a novel steel tool which sandwiches the wires under extreme pressure. The steel housing is then welded together and heat treated for over eight days. This creates a vacuum-like seal, similar to solder, yet cheaper, higher performing, and with a longer lifespan.
Applications:
- This device’s primary purpose is to form an electrical joint between two cable-in-conduit conductor wires, such as those typically used in superconducting magnets.
Advantages:
- The fabrication technique is simple, inexpensive, quick, and is designed to last as long as the CICC wire itself.
- Minimal electrical resistance compared to its predecessor, which allows a magnet to retain more power.
- Eliminates the need for solder, which is messy and leaves gaps in the electrical seal.
- Eliminates the need to handle the magnet after it has been heat treated, which lowers the risk to the brittle multi-million dollar magnet.
- Unlike previous methods, this joint technology will not need to be frequently maintained or replaced over the life of the magnet.
The present invention describes a method of fabrication for a low-resistance, vacuum-tight electrical connection for a cable-in-conduit-conductor (CICC) joint for use with a hybrid magnet. An elongate copper member is disposed in sandwiched relation between a first and second cable that are disposed in parallel, spaced apart relation to one another. A first elongate member is disposed in overlying relation to the first cable and a second elongate member is disposed in underlying relation to the second cable. All of the parts are positioned within a joint box, and the joint box is sandwiched between first and second flat plates that are interconnected to one another by elongate bolts. Tightening the bolts compresses the parts within the joint box. A heat treatment completes the solderless joint.
Advantages:
- Provides the low electrical resistances required for CICC magnets which in turn increases operational margins or decreases the cost of cryogenic refrigeration
- Eliminates the need for vacuum leak-tight copper to stainless steel mechanical bonds, which reduces the operational risk of vacuum leak and costly remediation
- Eliminates the need for solder filling, which reduces the risk during fabrication of the expensive superconductor typically costing more than $1m
- Eliminates the need for post-heat treatment processing, which reduces the risk of handling the expensive superconductor in its brittle state and reduces fabrication costs by eliminating lengthy and problematic solder filling processes
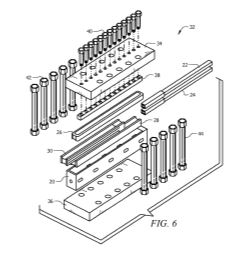